The high absorption of infrared light in silica is an established trait that has seen longwave infrared lasers operating at 10.6µm and 9.3µm implemented for a variety of applications over the years. In this article, we will look at three such use cases: laser damage growth mitigation, manufacturing of freeform micro-optics, and fiber optic processing. The partners we work with are leaders in their field because of the power and frequency stability reliably produced by our lasers.
Surface damage initiation of optical elements from near infrared lasers is a common issue that can quickly escalate as this is not a threshold event. Rather, it can be described as the probability of finding numerous damage sites per unit area of an optic as a function of the incident 3ω fluence on that optic. Once a damage site has been initiated, it can grow to a larger size, and growth is exponential with the total incident fluence quickly attenuating optical efficiency limiting component lifetime. To mitigate these effects a temperature stabilized AL50 longwave infrared laser can be used for non-ablative annealing which heats the glass to reflow and heal damaged sites locally. However, this is limited to the repair of shallow cracks just a few tens of microns deep at the 10.6µm wavelength because of its high absorption. For deeper damage sites a frequency doubled 9.3µm laser has been shown to provide excellent results up to 500µm in depth. This process is completed without generating debris and thus can be applied between polishing and finishing.
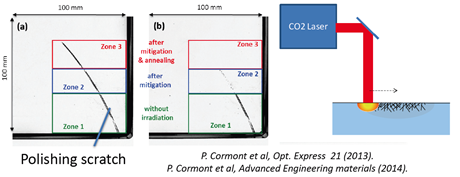
Figure 1: CO2 laser rapidly removes scratches via efficient melting of silica in a localized manner.
The second application of focus is laser direct-write micromachining which uses our high-performance light sources to manufacture freeform micro-optics for such end uses as high-powered diode laser optics. This is achieved through a high-precision laser milling process that first generates the required net-shape in a fused silica substrate, and then a second laser process generates an ultra-smooth, low-scatter, refractive surface. The direct-write machining process allows optical surfaces to be made that are fully customized to a particular application, often enabling complex systems to realize diffraction-limited performance. With power stability of less than +1% provided by the Access Laser Line Tracker feature, this micromachining technology has no symmetry restrictions, meaning new classes of optical surfaces can be created to fulfil requirements that were previously unobtainable. Generating smooth refractive surfaces in fused silica with sag up to 200µm.
Finally, one of the long-standing applications which Access Laser has excelled in is providing power and wavelength stabilized CO2 laser for fiber optic fabrication. Surface of silica fiber absorbs the CO2 laser energy strongly at 10.6µm wavelength band. This is a self-heating which is very different from the external heating used by traditional methods such as arc discharge, flame, and filament. The silica surface is a good absorption material for CO2 laser energy such that the beam hardly penetrates the interior of the fiber, and very little is scattered into the air. The heated fiber surface rapidly conducts the heat energy into the fiber inner structure, like external heating methods. The major difference from external heating methods is that a thin fiber will not be over heated compared to a thick fiber at the same CO2 power, since the thin fiber has less absorption surface area.
Figure 2: Examples of optical fiber elements fabricated by a laser heating system.
High power fiber lasers need a very clean fiber cladding surface, since most fiber laser designs use the entire glass inner cladding for energy delivery of pump laser power. High power splicing or long tapering times increases the probability of electrode or filament degradation, increasing risks of cladding surface contamination and power leakage. If such defects are introduced to the glass surface these contaminations will result in pump power leakage and may induce a critical failure at the location of splicers or tapers. CO2 laser heating eliminates the risk of metal deposition on glass surface as the absorption of CO2 energy is a gentle process that limits silica vaporization and re-deposition when well controlled. The subsequently produced smooth spliced fiber surface limits cladding power loss with conventional, low-index acrylate coated, double clad fibers.
With CO2 laser heating systems established as the best solution for splicing air-clad fibers to avoid the collapsing of air-clad structures using the appropriate light source is vital. Typical CO2 lasers with power stability of around +5% results in unpredictable splice losses and large ripples in the fiber or capillary tapering. Utilizing the temperature and optically stabilized laser features offered by Access Laser our partners have delivered hundreds of systems globally that continue to perform at the highest standard.